Projects
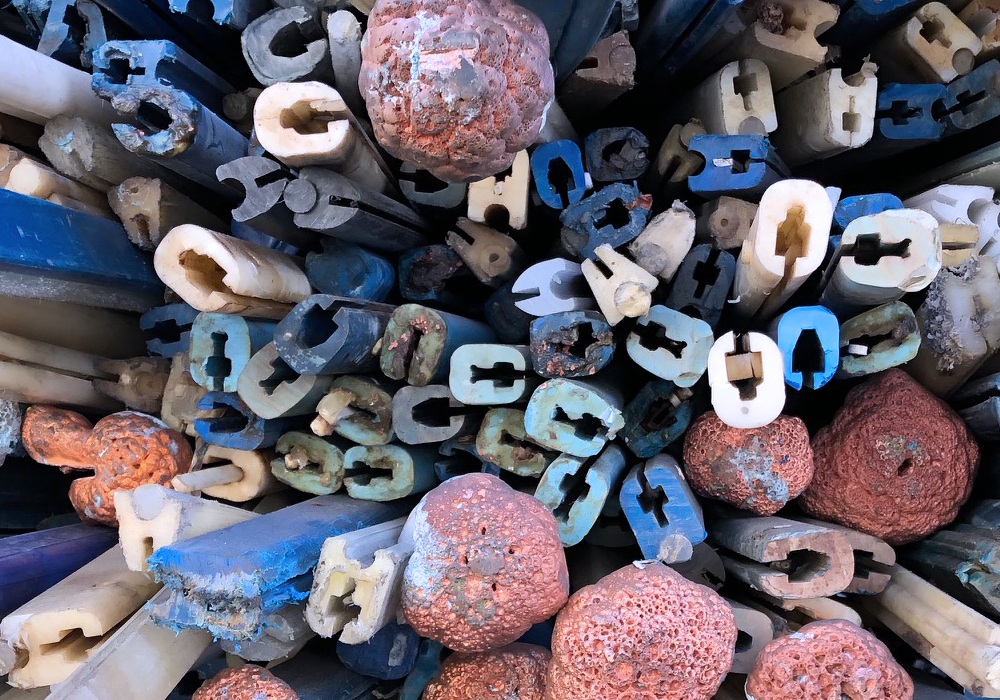
Cathode edge strips: Minor decision. Major implications.
by John Jickling, CEO
Decisions made at the design and supply stage of a project can have far-reaching consequences down the line. When it comes to cathode design, edge strips are a small but critical consideration that’s often overlooked upfront – but ends up having a major impact on safety, cost, productivity, and the environment.
Cathodes have an edge strip on each side to stop copper and other base metals from plating around the edges. When functioning properly, this allows the metal to be easily removed and processed. But not all edge strips are created equally, with performance varying greatly depending on the design, materials, and supplier.
Lifecycle comparison
Repairing 500,000+ cathodes a year gives us tremendous insight into which edge strips are winners and which ones aren’t. Low-cost edge strips on the market can seem like an attractive option, but they are often inadequately constructed, resulting in high failure rates and short life spans.
If you’re lucky, you might get 12 to 18 months out of them, but the long-term price will be much steeper than you bargained for. Now compare that to the type of edge strip we prefer to use, which easily outperforms the rest and consistently lasts 6+ years.
The hidden costs of “low-cost” edge strips
Poorly performing edge strips unnecessarily increase safety risk, waste, repairs, cost, and damage to the environment.
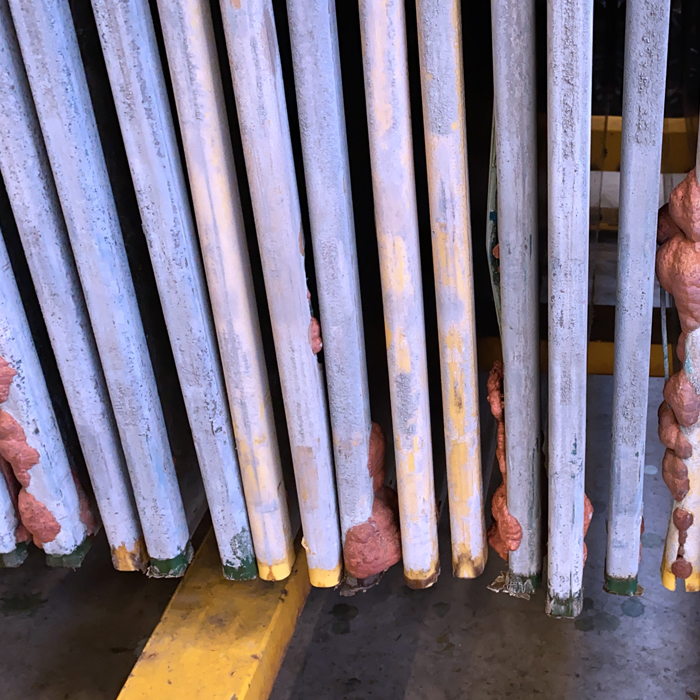
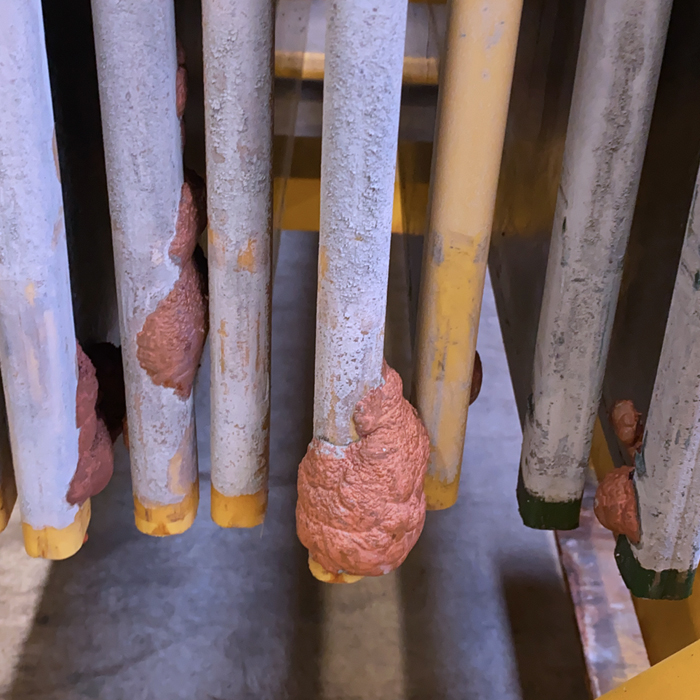
Examples of low-quality failed edge strips at our Tecnologias COBRA facility in Chile. Note the wrapped copper.
Increased tankhouse safety risks
Edge strips can be brittle and snap when they fail, making them difficult to remove. And edge strips that fail more frequently create higher safety risks, including:
- Increased interventions – unreliable edgestrips substantially increase the number of operator interventions required with automated cathode stripping machines
- Increased handling – each intervention requires additional loading and unloading from the process and increased material movement
- Added complexity and danger – failed edge strips cause base metals to plate around the edge of the cathode. In a best-case scenario, this results in the cathode blank being rejected – or more frequently, being damaged in the automated cathode stripping machine.
- Increase in handling risks – copper and cathodes are heavy, and awkward. Manually stripping base metals from cathodes that are plated around the edge creates needless safety risk to yourfor operators.
Operational disruption and cost
- Unnecessary damage and repairs – a damaged cathode will likely require repairs – which will generally exceed the cost of the edge strip
- Increased inventory – a higher number of cathodes will be required to compensate for ruined and out-of-service cathodes
- Lower grade copper/base metal – wrapped copper from edge strips can’t easily be removed, resulting in it being sold as off-grade production at a lower price
- Waste and unexpected cathode replacement costs – wrapped copper can result in destroyed cathodes that must be scrapped and replaced
- Increased labour cost and disruption – removing and replacing cathodes from the automated stripping system interrupts operations, requiring additional man hours and operational time.
Environmental impact
- Needless waste – potentially 4 times the amount of contaminated plastic waste that could have been avoided (based on expected life of 1.5 years vs. 6 years). This adds up to a staggering volume of tonnes of waste per year.
- Transporting new and damaged cathodes – significant increase in transportation required to replace destroyed cathodes and to perform off-site repairs on damaged cathodes
- Fuel and energy – substantially higher amount of fuel and associated resources required to repetitively remove and add cathodes to the system using industrial forklifts etc. Poor edge strip selection could potentially result in additional material movement of tonnes of cathodes, copper and plastic.
While we can and do install edge strips from all the major suppliers, our inside knowledge from decades of cathode repairs has repeatedly shown us which are the best and worst performers.
Our first choice for safety, performance, and the environment
Based on the results we’ve seen time and again, we recommend our clients go with Rochling edge strips – which deliver higher returns than anything else on the market. Unlike lower quality options, the material is produced by compression molding rather than extruded plate. A special sintering process is applied to limit material tension and enhance stability. Ultimately, they provide a tight tolerance, are highly durable, and are chemically resistant.
We’ve used this option with Glencore and Montanwerke Brixlegg with exceptional results, and are currently working with a number of Aurubis’ clients to make the switch.
Prevention is always better than the cure
What might seem like a minor decision can have a major impact on your people, profit, and the planet. It only makes sense to buy the product that lasts the longest and boosts productivity, while decreasing unnecessary waste, safety risks, and labour costs.
Learn more about our mining and mineral processing solutions.
Llevamos 20 años reparando nuestros cátodos exclusivamente con Tecnologías COBRA (The EPCM Group). Su tecnología y las reparaciones resultantes son insuperables por cualquier otra cosa en el mercado.
Sudamericano, SX-EW, Gerente de la Casa de Tanques